From pv magazine Global
New South Wales company Hysata is on track to commercialize the world’s most efficient electrolyzer, capable of producing green hydrogen for less than US$1.5 per kilogram by the ‘mid 2020s,’ it says. Moreover, the company believes it can reach gigawatt scale hydrogen production within a similar timeframe, saying its design is simple and suitable for mass manufacture today.
The company was born out of an electrolysis breakthrough made at the University of Wollongong, south of Sydney, around three years ago. There, researchers led by Gerry Swiegers discovered hydrogen could be produced far more efficiently using capillary-fed electrolysis.
This was verified in a paper published today in peer-reviewed scientific journal Nature, which found the capillary-fed electrolyzer could produce green hydrogen from water at 98% cell energy efficiency.
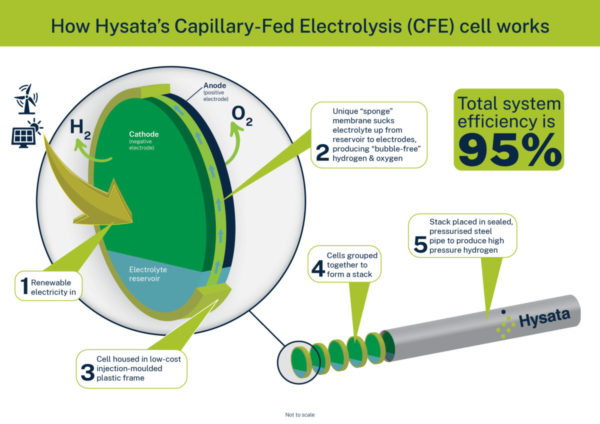
Image: Hysata
The Hysata electrolyzer consumes 40.4kWh of energy for every kilogram of hydrogen it produces. The Nature paper noted commercial electrolysis cells tend to use around 47.5kWh/kg, though Hysata CEO Paul Barrett claimed it was closer to 52.5kWh/kg. This equates to around 75% system-level efficiency, whereas the Hysata system claims a total efficiency of 95%.
This 20% efficiency boost has enabled the massive cost reduction Hysata says it’s only a few years away from making a reality. “You really collapse the project economics through that efficiency lever,” Barrett told pv magazine Australia. The academic added the company has “a simplified system which really reduces the cost quite substantially.”
Cost
Barrett didn’t want to commit publicly to the price of the Hysata electrolyzer, but said the company is in conversation with around 30 “name brand companies,” needing green hydrogen, who are “thrilled” about the economics.
“Our technology will enable hydrogen production of below US$1.50 per kilogram by the mid-2020s, meeting Australian and global cost targets much earlier than generally expected,” Barrett said.
Barrett said the company is busy building its pilot line of electrolyzers in a house near Wollongong now. “We’re building a huge test capacity, like, today,” he said. He is hoping to begin testing them in parallel within the next few months, with plans to ramp up the pilot line in 2023.
From pilot scale, the company wants to jump directly into gigafactories. To enable this, Hysata will grow its team of 20 engineers significantly this year.
“We are planning to have systems in the field by 2025,” Barrett said.
“I’ve got plates working today at the efficiency and performance that we’ve got on that paper,” he added, referring to the study in Nature, and adding: “our next thing is to basically string lots of those together, not unlike the way you’d string multiple solar modules together. We’ll connect them in series and that becomes our stack.”
The company “certainly” plans to keep its manufacturing in Australia, Barrett said, possibly remaining in Wollongong – which is right next door to the proposed Port Kembla hydrogen hub.
“This can be an era defining company for Australia,” the CEO said, noting that Australia imports the vast majority of its renewables equipment today, such as solar panels and wind turbines. “There’s a real opportunity to build sovereign manufacturing capacity here in Australia and export it to the world,” he added.
This very much aligns with Matt Kean’s plan, the state’s environment and energy minister as well as treasurer. In February, he announced AU$250 million (US$180 million) in funding to boost locally manufactured renewable energy content and a further AU$300 million (US$216 million) to build a renewables-powered manufacturing base including renewable hydrogen.
The company is the “first in the world” to commercialize a capillary-fed electrolyzer, according to Barrett. To date, he says, electrolyzer technology has been “too inefficient and too complex” to make green hydrogen attractive. Hindering efficiency in electrolyzer cells is resistance, which has typically come from bubbles which are non-conducting, and mask electrodes.
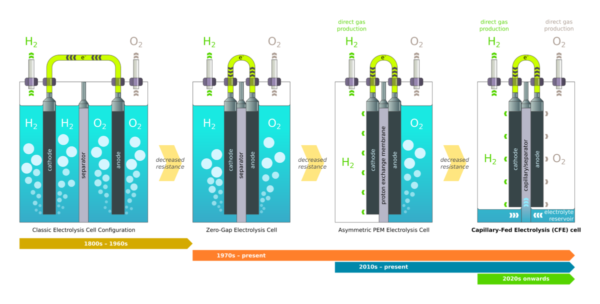
Barrett said the research team at the University of Wollongong “basically looked at that problem with a blank sheet of paper and really tried to understand where all the resistance is, inside the cell.” That exercise led to the invention of capillary-fed electrolysis which eliminates these bubbles and boosts efficiency.
This leads to a “double whammy benefit on the economics,” Barrett says, because hydrogen projects would need less renewables to get the same hydrogen output, saving on capital outlays while also only needing to purchase a smaller electrolyzer.
Electrolyzer details
The company’s electrolyzer is fives times smaller than a traditional alkaline electrolyzer, Barrett says, and contains 20 times less liquid. It fits inside a six-meter shipping container and can be moved by forklift for easy transportation, he added. “So we’ve got a drastically simplified balance of plan.”
Hysata’s electrolyzer cell frame is made using a scalable, low cost and mass manufacturing technique – making the product nimble so it can get to market as quickly as possible.
“We’re one of the few, if not the only, electrolyzer from time zero, to be mass manufacturable,” Barrett said.
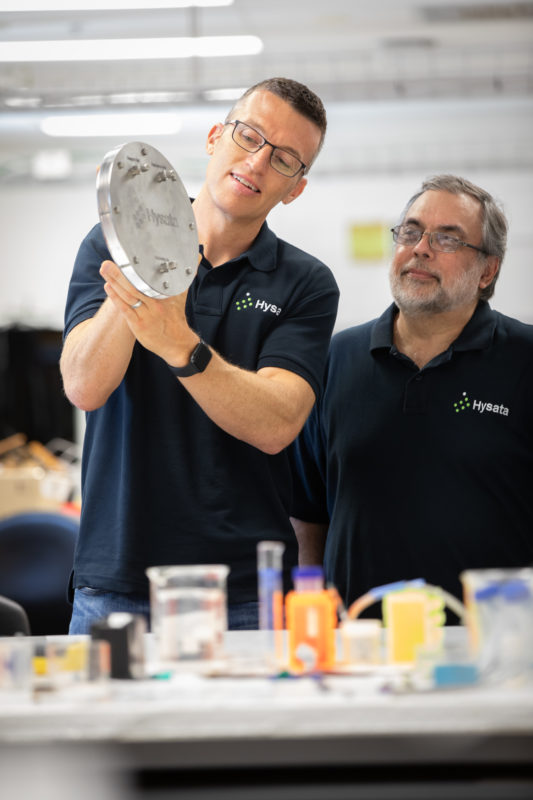
Image: Hysata
Hysata, a start-up, only officially launched in June last year. It kicked off with AU$5 million (US$3.6 million) in seed funding from the UK-based IP Group, with AU$750,000 (US$539,000) from the government-owned Clean Energy Finance Corporation (CEFC).
Swieger, who led the University of Wollongong ARC Centre of Excellence for Electromaterials Science research, has since become Hysata’s chief technology officer.
This content is protected by copyright and may not be reused. If you want to cooperate with us and would like to reuse some of our content, please contact: editors@pv-magazine.com.
By submitting this form you agree to pv magazine using your data for the purposes of publishing your comment.
Your personal data will only be disclosed or otherwise transmitted to third parties for the purposes of spam filtering or if this is necessary for technical maintenance of the website. Any other transfer to third parties will not take place unless this is justified on the basis of applicable data protection regulations or if pv magazine is legally obliged to do so.
You may revoke this consent at any time with effect for the future, in which case your personal data will be deleted immediately. Otherwise, your data will be deleted if pv magazine has processed your request or the purpose of data storage is fulfilled.
Further information on data privacy can be found in our Data Protection Policy.