A report by IDTechEx shows a shift towards higher nickel-content nickel-manganese-cobalt (NMC) lithium batteries for electric vehicles over the last few years. Chinese battery maker SVOLT has reportedly begun series production of their NMX cells, French car manufacturer Renault has announced its strategy would rely on NMC cathodes. SK Innovation announced intentions for commercial production of NMC cells using 90% Ni during 2021. SK Innovation also stated their plan to have developed a 94% Ni NMC by 2025, highlighting a continued place for NMC but also highlighting the difficulty in moving toward ever higher nickel, and ever lower cobalt content NMCs.
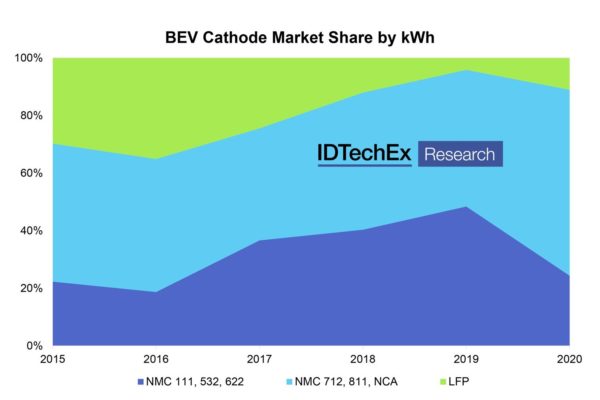
IDTechEX
However, there was also a resurgence for lithium ferro phosphate (LFP) in 2020 and certainly, the chemistry has gained added importance. Automotive OEMs have come forward with plans to use the chemistry due to its lower cost and added safety, while the imminent expiry of IP relating to LFP will make it easier to manufacturer and export LFP outside of China.
Nevertheless, IDTechEx consider layered oxide materials, such as NMC and Lithium Nickel-Cobalt-Aluminum Oxide (NCA0, to remain central to the success of vehicle electrification given the added range they provide. Beyond cars, a range of chemistries is utilized and offered by manufacturers with choices coming down to application requirements and regional preferences.
Market
Overall, worldwide electric car sales were stronger than expected in 2020. Additionally, investment continued to pour into electric vehicles and Li-ion batteries with 2020 seeing an additional 200 GWh of planned capacity announcements in Europe – this figure continues to grow on a regular basis in 2021. The past year has also seen Tesla, Volkswagen, General Motors, SK Innovation, and LG Chem all come forward with investor days and presentations outlining their vehicle electrification and battery technology strategies, all of which adds to the growing momentum behind the electric vehicle market.
Battery design
Shifts in battery pack design are also taking place. For example, 800V architectures have been adopted by a number of OEMs, driven by promises of fast charging and more efficient operation. However, the necessary charging infrastructure also needs to be in place to fully utilize this and the battery itself will need to be able to handle increased fast charge powers. Greater care will also be needed to ensure electrical isolation of the battery pack while the necessary shift from Si to SiC inverters comes with its own costs.
Cell-to-pack (CTP) designs are also being explored. Here, the greater packing efficiency can help overcome the energy density reduction that comes from LFP with BYD, CATL, Tesla and Stellantis all announcing their intention to use LFP cathodes (perhaps LMFP in Stellantis’ case) in combination with CTP battery designs. However, outside of electric cars, modularity remains important, with most pack manufacturers in Europe and North America offering modular designs. The added redundancy and repairability take on added importance in commercial sectors while the design also allows pack manufacturers to serve multiple vehicle segments more easily.
Of course, cathode chemistry and battery structure are only parts of the puzzle. Cell design and form factor, solid-electrolytes, anode material choices, thermal interface materials and battery management systems all form part of the battery design ecosystem with numerous avenues for improving battery and EV performance, cost, and safety.
An array of technological possibilities, and a diverse set of design choices, are opening up in the battery and electric vehicle landscape. For analysis on the developments in battery and electric vehicle technology and markets, please see the report “Lithium-ion Batteries for Electric Vehicles 2021-2031“.