From pv magazine 05/2021
Plant owners need to invest in recombiner monitoring equipment or pay more for maintenance in the long run. The string-level monitoring sensors are placed right into the combiner boxes across the array, as pictured here.
Drones and artificial intelligence have caught the attention of businesses and customers across many industries. In Spain, Ingeteam’s service division has trialed the combination of the two to further drive down monitoring and maintenance costs. But even with these novel approaches, there seems to be no way around monitoring granularity.
This discussion has previously arisen when manufacturers of string inverters and module-level power electronics attempted to point out the perks of their respective products. However, between central and string inverters, this contention did not seem to have taken place. The reason has been either a lack of relevance or a large enough market for both.
Together with the University of Castilla-La Mancha, in the city of Ciudad Real, Ingeteam equips drones with thermographic cameras to detect hotspots and other temperature abnormalities in solar projects. The thermographic video of the drone flight is then analyzed with a proprietary algorithm and matched against SCADA data coming from the inverter.
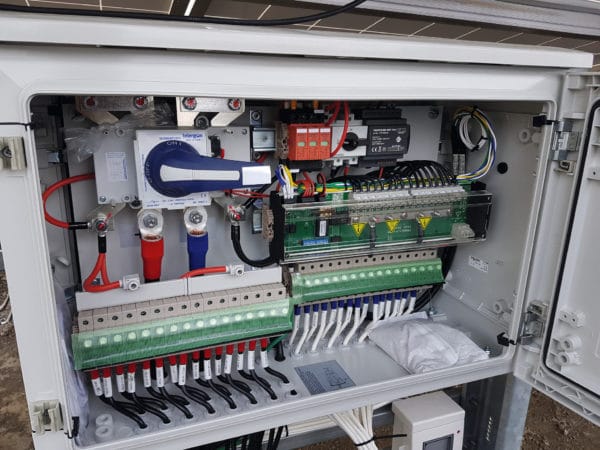
In the past, project owners had to invest large sums to capture thermographic images, but this problem can now be addressed using drones. “But then you [still] have to evaluate the images, which costs a lot of time,” Antonio Fernandez-Diez, R&D manager of the service division at Ingeteam, told pv magazine. He added that a current challenge is a lack of data granularity from the inverter.
In this first trial, the team tried the technology on a project using central inverters. A second trial will provide insights into whether string inverter-based projects can offer higher data granularity and improve fault detection.
Breaking down breakdowns
Solar power plants are fully exposed to the elements, and as with any other type of technology, the occasional hiccup is inevitable. Burned bypass diodes are a classic problem. And while it is easy to think that a small diode failure at a big plant won’t break the bank, the reality may differ. Assuming burned diodes take a few weeks to detect and repair, and cause a performance ratio loss of a mere 4%, the damage could easily reach over €40,000 for a 5 MW site due to lost revenues, as well as the troubleshooting and repair costs.
The performance ratio loss isn’t significant, and therefore detecting the fault is not an easy task. Higher granularity should provide for much-improved fault detection, faster and more targeted repair, but string inverters don’t automatically provide higher granularity. The level of monitoring detail is driven by the project developer’s willingness to invest in additional electrical measurement equipment.
“In the field of monitoring, we see that in the often-used string inverter power class between 30 and 100 kW and higher, the inverters perform measurements only on MPPT level and not string level,” said Jonas Riexinger, EVP technics and operations at monitoring service provider meteocontrol. However, he adds that it is manufacturer dependent. The lack of string-level monitoring in string inverters is not surprising, seeing that today’s models reach beyond 300 kW power ratings and have become as powerful as central inverters some years ago.
String inverter growth
String inverters have been creeping into the utility-scale market segment for some years now. This development is also reflected in the new product portfolios of string inverter suppliers, as an increasing number of manufacturers take 200 kW and 300 kW-plus string inverters to market. “We are witnessing that, especially in Europe, there are only very few new projects using central inverters, compared to 10 years ago,” says Riexinger.
Fernandez-Diez adds that one of the frequently raised arguments in favor of string inverters has been their low servicing cost. But this is only true during the warranty period, the R&D manager says. Service crews can swap faulty units. Broken central inverters, of course, need to be serviced, often by the manufacturer’s staff. Following the warranty period, Fernandez-Diez claims, string inverter repairs are more costly than the service for central inverters.
By default, the inverter – string or central – provides insight into key metrics like the IV-curve and string current level, for example. These metrics can help to identify problems. But depending on the model, the data can be limited, and granularity might be on maximum power point tracking level. To achieve greater detail, project developers must install additional string-level data logging devices into the combiner boxes. Some project developers have omitted this step in the past.
Software solutions
Combined with sensors for irradiation, diffuse light, and temperature, modern monitoring software can estimate what the power plant should produce. A deviation of this performance expectation can then be interpreted by a monitoring engineer, or an algorithm, to determine what type of failure is at hand. At the string level, it is also possible to compare two adjacent strings with one another. If there is a deviation in the performance, the lower-performing string might need a service.
“I think monitoring is always a balancing act between capex and opex,” says Riexinger. “This means that there is the choice to save cost on monitoring equipment, but this will then increase overall maintenance costs.” He adds meteocontrol has solutions to work with any type of plant architecture, of course, but that from a monitoring perspective string-level monitoring has many advantages to ensure the yield.
A central inverter typically has only about one or two maximum power point tracking inputs, despite a power rating of three or more megawatts. In terms of monitoring, central inverters often come with in-built, so-called zone monitoring. Measurement then happens per input channel on the MPPT level. Detecting a performance ratio loss of less than 5% at this granularity is a tall order. Substantial amounts of data noise can obstruct a clear interpretation of the monitoring data.
Clouds, cable length, structural shading, and module angle could impact string performance, making it harder to find a single burned bypass diode in an enormous array. Comparing the performance of a batch of 24 strings placed on a single MPPT channel against another set of 24 strings on another channel makes detecting smaller failures complicated.
“For MPPT monitoring, for example, 10 individual strings will be represented by one current value. So, operators don’t necessarily conclude that there is a problem at hand considering a certain variance if there is a failure in only one string. This accumulates to a bigger loss,” Riexinger says.
Losses add up
Data analytics company Raycatch puts some perspective on what this loss can mean. Earlier this year, in a white paper, the company analyzed the performance of 75 sites comprising 1.2 GW. On average, each site was underperforming by just over 5%. In their findings, Raycatch also pointed at several plants which used combiner box level monitoring, which suffered from whole strings being detached without the combiner box monitor system sounding an alarm. Reportedly, the average annual financial losses would be to the tune of $160,000, assuming the average plant had a capacity of 16 MW.
There is little doubt that string monitoring is better to detect faults in an array. And, in combination with thermographic drones, Fernandez-Diez explains that he believes, but needs to confirm, that the combined data is theoretically better. Since the end of 2020, Ingeteam and Fernandez-Diez have sought to establish any monitoring efficacy improvement on the back of inverter choice. The team will have to wait another two years before he can bolster his claim with reliable data, as the current research project will last through to September 2023.
Costs and incentives
Cost efficiency of the O&M solution plays an important role – the best possible approach is not always the one that is the most desirable for fleet owners. Something that becomes evident when comparing monitoring approaches in markets with different financing and remuneration models.
In the U.S., for example, recombiner monitoring is much more prevalent than string level monitoring. “There is a lot of price pressure, of course,” says Riexinger. “In the U.S., the expected depreciation of utility-scale solar plants is less than ten years. In Germany, on the other hand, projects receive a feed-in tariff for 20 years.” Thus, German plant owners are incentivized differently, and therefore, primarily use string monitoring.
Maintenance decisions
Project owners may not always want to immediately repair faulty parts that incur just a minimal performance ratio loss. Sending out a truck roll to swap a few underperforming modules at a more than 100 MW site could cost more than waiting to fix the modules at the next scheduled service. At Ingeteam, one of the research aims is to create a system that can give clear advice about what needs to be fixed and when.
“We are mixing not only the data from the thermograph images and SCADA records but also from exogenous information like the price of energy, and Ingeteam’s proprietary data from maintenance interventions” explains Fernandez-Diez. The monitoring system can then calculate the most lucrative moment to repair problems, as well as the cost of the intervention. A decisive advantage compared to other drone and algorithm-based solutions, he says.
Again, to provide this kind of insight, the R&D manager and his team found higher monitoring granularity to be essential. “What we are looking for is correlating defects on a panel with the data from the inverters,” he says. “With central inverters, the defects become quite diluted in this amount of capacity.”
While Fernandez-Diez and his team focus on analyzing the data collected by the inverter and the drone, other types of data could also be collected by drones. For example, adding an electroluminescence camera to the drone may further improve the fault detection algorithm. “We haven’t done EL yet, but that is on my to-do list,” he says. “It is a growing technology, and there are techniques that have evolved a lot.”
This content is protected by copyright and may not be reused. If you want to cooperate with us and would like to reuse some of our content, please contact: editors@pv-magazine.com.
1 comment
By submitting this form you agree to pv magazine using your data for the purposes of publishing your comment.
Your personal data will only be disclosed or otherwise transmitted to third parties for the purposes of spam filtering or if this is necessary for technical maintenance of the website. Any other transfer to third parties will not take place unless this is justified on the basis of applicable data protection regulations or if pv magazine is legally obliged to do so.
You may revoke this consent at any time with effect for the future, in which case your personal data will be deleted immediately. Otherwise, your data will be deleted if pv magazine has processed your request or the purpose of data storage is fulfilled.
Further information on data privacy can be found in our Data Protection Policy.